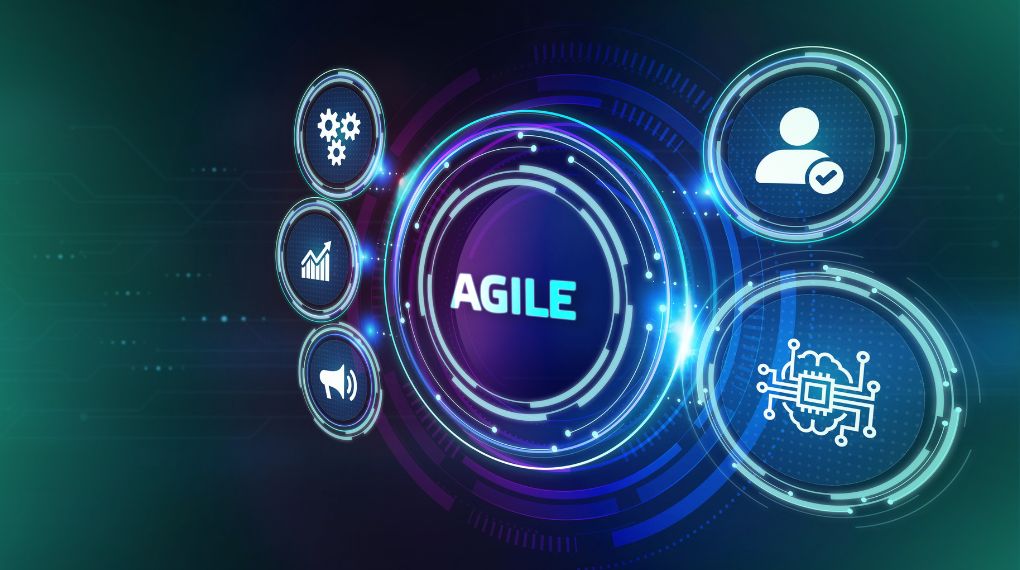
• Morning:
o Introduction to Lean Principles: Value stream mapping, 5S methodology, waste elimination.
o Six Sigma Concepts: Defining Six Sigma, understanding variation and defects.
o Introduction to DMAIC Methodology: Define phase – project charter, scope definition, customer requirements.
• Afternoon:
o Lean Thinking Tools: Poka-Yoke, 5S implementation, visual management.
o Six Sigma Tools: SIPOC diagram, process mapping, VOC (Voice of the Customer) analysis.
• Morning:
o Data Collection Methods: Process observation, data logging, surveys, interviews.
o Data Analysis Techniques: Descriptive statistics, data visualization, histograms, Pareto charts.
o Key Performance Indicators (KPIs): Identifying and measuring critical process metrics.
• Afternoon:
o Data Analysis Tools: Statistical software (e.g., Minitab, Excel), data analysis techniques.
o Hands-on Exercise: Data collection and analysis for a real-world process.
• Morning:
o Root Cause Analysis: Fishbone diagrams, 5 Whys analysis, Failure Mode and Effects Analysis (FMEA).
o Process Variation: Understanding and analyzing process variation using statistical tools.
o Design of Experiments (DOE): Identifying key process inputs and their impact on outputs.
• Afternoon:
o Hands-on Exercise: Conducting root cause analysis for a process with defects.
• Morning:
o Developing and Implementing Solutions: Brainstorming, creative problem-solving techniques.
o Lean Tools for Improvement: Kaizen events, SMED (Single Minute Exchange of Die), value stream mapping.
o Six Sigma Tools: Design of Experiments, simulation modeling.
• Afternoon:
o Hands-on Exercise: Developing and implementing improvement solutions for a case study.
• Morning:
o Control Plans: Developing and implementing control plans to sustain improvements.
o Monitoring and Measurement: Tracking KPIs, conducting periodic reviews, and making adjustments.
o Continuous Improvement: Building a culture of continuous improvement within the organization.
• Afternoon:
o Lean Six Sigma Project Presentations: Participants present their project findings and recommendations.
o Q&A and Wrap-up Session